A Prescription for Innovation in Biopharmaceutical Manufacturing
Organizations developing and manufacturing life-saving treatments are consistently tasked with accelerating patient delivery while being fully compliant with regulations.
NecstGen, the Netherlands Center for the Clinical Advancement of Cell and Gene Therapies, specializes in manufacturing Viral Vectors and Cell Therapies. The organization recognizes the benefits of being a digital facility because integrating data and systems are key to delivering new therapies.
In pharmaceutical manufacturing, advanced lab equipment often exceeds simple standard software’s ability to share, connect, and manipulate data.
NecstGen needed a bridge between their complex development and manufacturing work and the operational technology. Low code presented a way to connect systems while staying compliant, managing data, and providing an integrated view of laboratories and cleanrooms.
In 2020, NecstGen adopted the Mendix low-code development platform. Since then, they have maintained compliance with stringent pharmaceutical production standards while simultaneously streamlining their laboratory and cleanroom processes and enhancing data quality.
A Low-code Remedy
In the realm of biotechnology research, production and testing, any disruption – whether in actions or data accuracy – carries significant consequences.
“Our products are administered to patients. That is a huge responsibility,” shared Kees Mensch, Head of IT at NecstGen.
NecstGen, functioning predominantly as a Contract Development and Manufacturing Organization, stands out by targeting academic groups and smaller startups to help materialize their innovative ideas. “There is a market gap for a targeted, dedicated, and smaller scale to accelerate good ideas from development to clinical trials,” highlighted Lindsay Mulder, Viral Vector specialist at NecstGen.
NecstGen’s focus extends on Cell and Gene Therapy, placed at the crossroads of manufacturing excellence and data-driven pharmaceutical innovation. Yet, despite the use of sophisticated tools in its Viral Vector and Cell Therapy laboratories and cleanrooms, challenges do arise.
Equipment can often be from multiple suppliers or have inherently rigid software. Therefore, a flexible solution connecting the system landscape was needed, a new addition to their IT infrastructure.
When exploring adaptable software solutions, NecstGen sought a platform that could:
- Standardize data capturing from their digital equipment to enhance data quality
- Optimize their lab’s Viral Vector processes and eliminated paper-based processes
- Comply with the European Union’s strict Good Manufacturing Practice (GMP) requirements
“There is a lot of specialized equipment in the laboratories and cleanrooms that need to be completely foolproof so there are no mistakes made when working with viruses, cells and chemicals,” Mensch explained.
Mendix was selected due to its:
- Innovative and collaborative nature
- Flexible and strong architecture
- Modern integration capabilities
“The interesting thing for the scientists is that they could experience a nice journey to make a product with Mendix. And for a developer, understanding the ins and outs of the lab’s operating procedures was critical to creating those unique solutions,” Mensch said. “Their worlds collided with the introduction of Mendix.”
Enhancing Viral Vector Processes
In 2023, Mulder presented a business case aiming to streamline lab operations to Mensch and Erik Bottenberg, Tech Lead and Architect.
A collaborative team of seven, then began developing three low-code applications, including a cell tracker for the Viral Vector lab, a clean room dashboard, and a transactional layer that communicates with third party software to protect their Laboratory Information Management System (LIMS).
Simplifying Big Data
Given NecstGen’s focus on individual and critical patient treatments, specialized equipment is used.
Cell culture is an essential part of production processes executed at NecstGen. Therefore, the equipment analyzing cell number and viability plays a central role in providing information on quality of the cells used in these processes.
“The equipment assesses many aspects of the physical condition of the cells. It can assess how many are alive, if they are clumped together, or not, their size and shape is among other things. This is all vital information for our processes,” Mulder explained. “And because we are running large optimization experiments, we could be testing many, many different conditions to produce pharmaceutical Viral Vectors.”
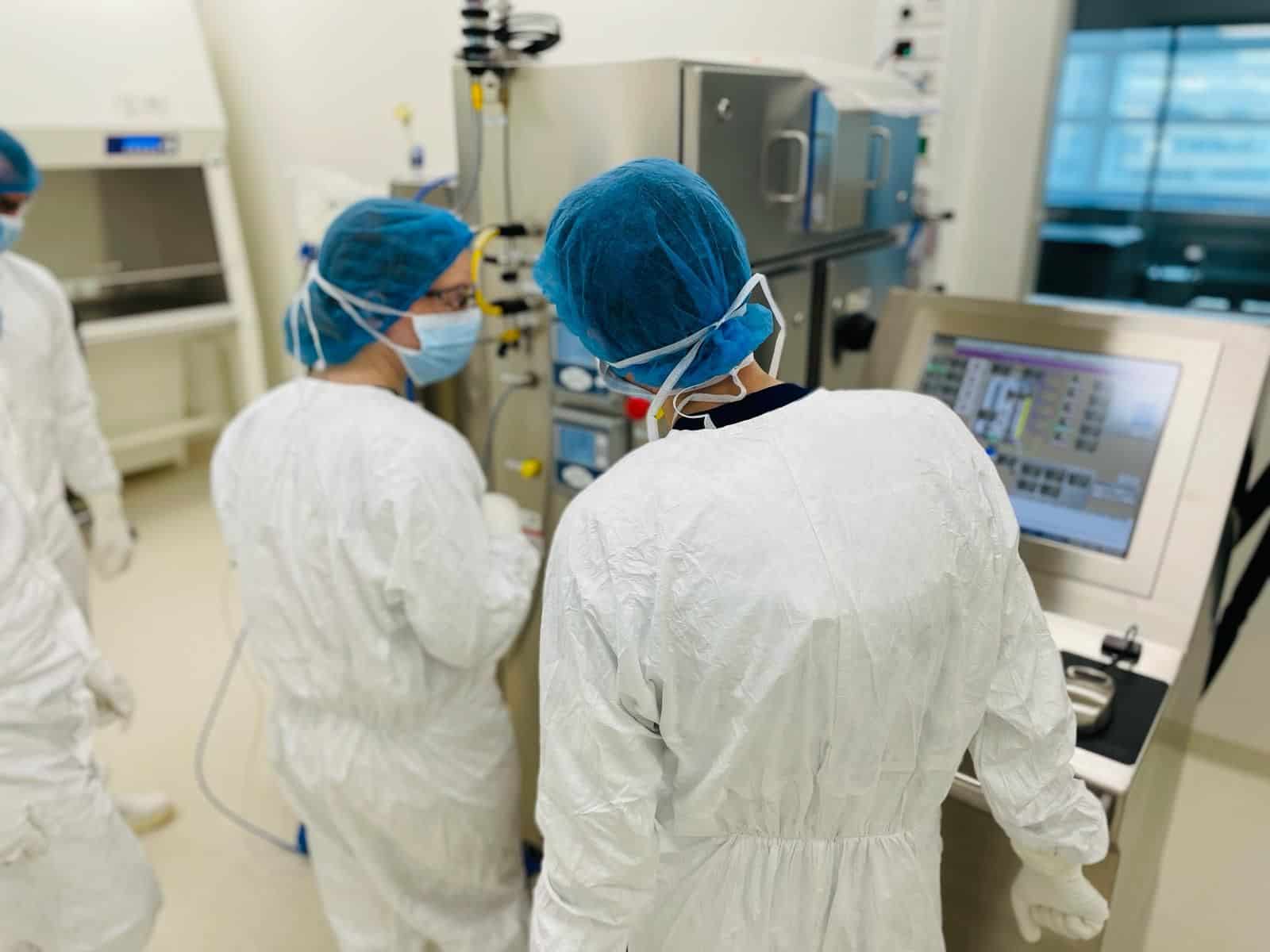
NecstGen’s cell analytical equipment, while impressive in their primary function, lacked built-in data analysis capabilities, generating only CSV files that proved challenging to manipulate in Excel.
“Because of many needs – equipment optimization, new variants – and that GMP regulations are very rigid, it may take lots of time and money for a manufacturer to update their software and equipment. And some equipment is standalone, there is no ecosystem integration” Mulder said.
Using Mendix, NecstGen developed as a proof-of-concept NucleoTracker, an application that eliminates manual data collection. The new, user-friendly solution improved the Viral Vector team efficiency, streamlining their data collection process. NucleoTracker’s features include:
- Table sorting functions based on dates, samples, and viability.
- Export capabilities to Excel to create graphs and trends from the data.
- Automated calculations over designated time periods, offering insights into the performance of cultures.
- Automated sample grouping, streamlining the organization and analysis of data points.
With Mendix, the initial concept version of NucleoTracker was delivered in just one week. Since then, Mulder and Bottenberg regularly collaborate to make improvements and expansions, leveraging tools like the Feedback widget from Marketplace.
Even with ongoing modifications and validations of the application, Mulder is already seeing tangible results.
A New, Digital Cleanroom
Cleanroom monitoring is critically important in a GMP environment, requiring extensive maintenance and continuous oversight. To ensure a quality environment for processes and samples, NecstGen developed a dashboard in Mendix that:
- Centralizes information about data and sample collection
- Offers dynamic overviews assessing location conditions
- Incorporates business rules to prompt actions when a specific threshold is exceeded
“You can search all the cleanrooms and find the nitty-gritty details about monitoring sessions, asset information, calibration dates, maintenance schedules, and project managers. The application also supports high-level reporting about all NecstGen premises or specific subsets.” Bottenberg explained.
“Most importantly, they can more easily receive integrated automatic alerts based on organizational requirements from the data we’re now able to retrieve.”
For Mensch, showcasing the real-time status of a cleanroom during a call using Mendix is impactful. “This immediate visibility, in comparison to delayed paper documentation, builds trust,” he said.
Maintaining Compliance
NecstGen’s final application of Mendix is in the form of a controlled, transactional layer positioned between the LIMS and procurement software.
“We already have a compliant system of record that are difficult to alter, given in this line of work, so we are using Mendix as a system of and integration,” Mensch shared.
This layer helps NecstGen to provide customers access to their findings without granting direct entry into the LIMS system. Additionally, the platform’s security capabilities come into play when the departments order materials, preventing unauthorized transactions or supplier updates from infiltrating their systems.
Better Data Unleashes Innovation
The most significant advantage of integrating Mendix into NecstGen’s IT infrastructure is the improvement in data use, analysis, and sharing.
“Some equipment produces tons of data, while others provide very little,” Mensch said.
Maintaining a strict separation between external, unstructured data and the new structured format used by NecstGen ensures everything is uncompromised. Since roughly half of the lab and cleanroom equipment is readable by Mendix, the scientists have more control over their data, remaining compliant, flexible, and innovative.
“Our ability to share this intelligence internally is strong, too,” Mensch emphasized. “Each team member, with their unique background, focuses on different aspects of the data. This diversity makes the collective power of our insights even stronger.”
“There are already new Mendix projects in the works for processes such as quality assurance and customer journey support,” Bottenberg added.
Accelerating Patient Impact
NecstGen is at the forefront of the pharmaceutical manufacturing landscape with tools like Mendix, providing trustworthy data, ample integration capabilities, and thorough oversight.
“We are really elevating the way we work within our organization,” Mensch said. “This equipment can range anywhere from tens to hundreds of thousands of euros. By enhancing our data capabilities, we are making sure everything is structured for the future.”
Mulder advises fellow specialists in the industry exploring low-code to “identify the specific problem, delve into the root cause, and start very simple.”
From the developer perspective, Bottenberg added, “You truly need to understand your customer’s processes and identify what about the current system is impeding their workflow, causing unnecessary time consumption or potential errors. Investigate the possibilities together with them and immerse yourself completely to make the biggest impact.”
“Then you can have the right discussions with the users to create the best solutions. In this industry, value comes from letting innovation and compliance work hand in hand,” he said.
Continuous improvements and additions to NecstGen’s low-code applications are reinforcing the organization’s commitment to keep patient therapies at the center of their work.